Injection Rubber Group ( also known as IRI ) was founded in 1990 with its head office in Taipei, it has large-scale manufacturing sites in Dongguan and Suzhou. IRI has been specializing in Liquid Silicone Rubber tooling design and fabrication, LIM molding, overmolding and compression molding for more than three decades.
It is one of a few large and time-honored manufacturing groups in China who can carry out LIM molding, silicone rubber compression molding and tooling design and fabrication in house.
IRI Dongguan factory is located in Dongguan, China with total land area of 22000 square meters. It boasts garden-like working environment with staff size of around 400 employees.
Over the past years, IRI has been working to meet diversified market demand, our parts have been customized for different applications and widely used on such areas as automotive, consumer electronics, new energy, medical care, and daily houseware etc. Mainly including keyboard rubber sheets, membrane,silicone seals and gaskets used on automotive connectors or harness, Bluetooth silicone parts, smart wearable device silicone parts , overmolding parts, keypad used on car door, laryngeal mask, nebulizer face mask, nasal mask and other silicone medical parts, silicone nozzle, shower head and other houseware silicone parts etc.
To satisfy our customer demand, our molding workshops have been equipped with LSR vertical injection molding machines, Arburg horizontal LIM Molding Machine, and Silicone Rubber Compression Molding Machines. We have also set up full-grown tooling fabrication workshop in which there are such tooling building equipment as CNC milling machines, turning machines, EDM, automatic grinding machines and other drilling and milling machines etc.
Clean Rooms have been especially set up for molding medical parts, consumer electronics precision parts and cosmetic parts, and silicone baby products.
As one of leading LSR Injection molding Companies, IRI places high value on technical innovation. IRI R&D team have been exploring and practicing state-of-art tooling concept and process, and have become the first one in mainland China who carries out automatic, No-Flash Molding process in terms of LIM molding. Un-manned, full automatic, and no-flash injection molding process has been successfully implemented with smart monitoring system throughout the whole production, this has been helping a lot in cost-efficiency, capacity as well as better quality assurance. Smart CCD has also been introduced to make our final quality inspection intelligent, automatic and more efficient.
IRI attaches great importance to quality, and has set up sound quality control system. Such quality certificates as ISO 9001: 2015, ISO14001, ISO 13485 and IATF16949 have been obtained.
IRI has been strictly implementing quality system standards in all company aspects. Quality department has been armed with such inspection device as profile projector, CMM, hardness tester, force Tester, life cycle tester, Rohs Analyzer, and Smart CCD etc.
IRI has established long-term partnership with world-renowned companies home and abroad, most of our customers are world-leaders in the field of automotive, consumer electronics, and houseware etc
IRI is always dedicated to pioneering the technical innovation in the field of LIM molding, providing customers with more competitive prices and high-quality products. We look forward to working together with customers home and abroad to usher in better future!
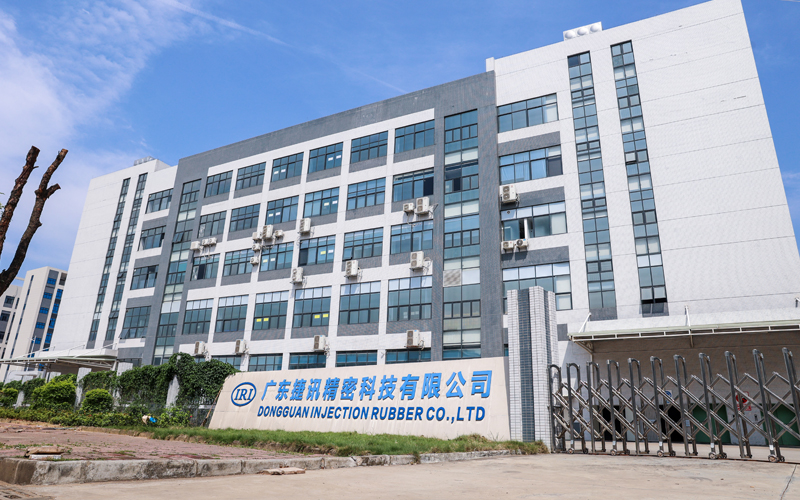
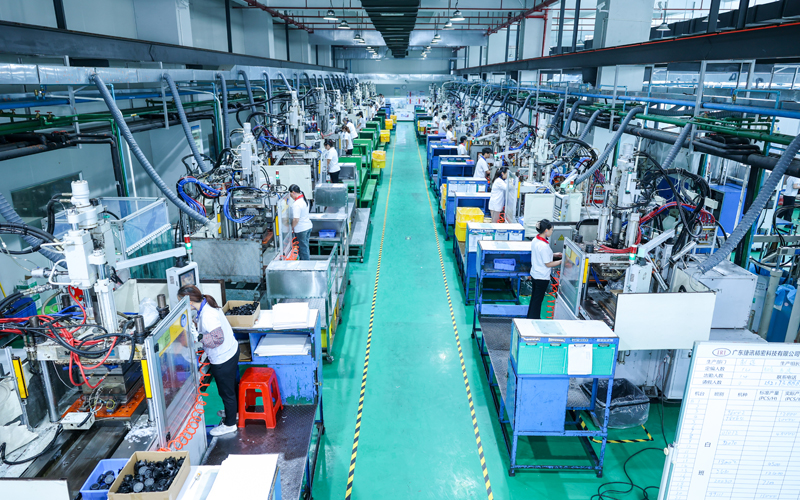
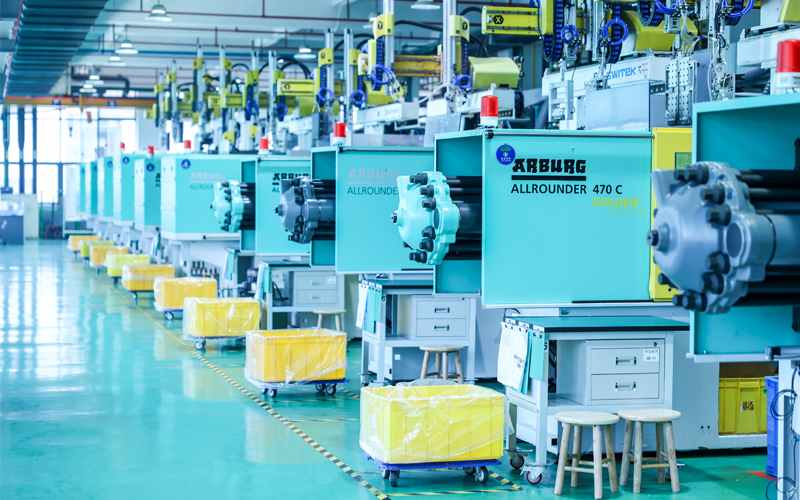
|